Papermaking Technology
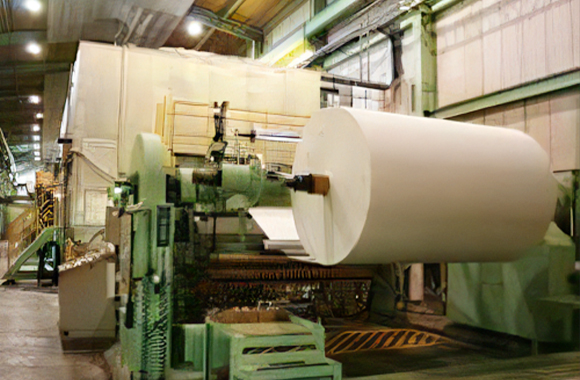
We create products using a wide variety of papermaking technologies, such as high-density, small-lot, density-gradient, sparse and dense, long-fiber, and low-concentration papermaking, as well as powder fixation.
We have cultivated these papermaking technologies since our establishment based on our ability to newly install and improve the equipment according to market needs and to take advantage of the equipment. Let us introduce our technical processes of preparation of raw materials, wire part, and dryer part.
- High-density papermaking
- Preparing raw materials creates high-density paper.
- Small-lot papermaking
- We can conduct mass production from as small as approximately 500 kg of raw materials prepared.
(It varies depending on the product specification conditions.) - Sparse and dense papermaking
- Low-density and high-density paper can be made alternatively on the same paper.
- Long-fiber papermaking
- Fibers that are up to approximately 10 mm in length, such as synthetic resin, can be used for papermaking.
- Low-concentration papermaking
- Since raw materials can be used at extremely low concentrations for papermaking, paper with superior dispersibilitya nd uniform texture ca n be manufactured. Therefore, long synthetic fibers can be used for manufacture.
- Powder fixation
- Powders can be fixed to the main raw material in papermaking.
Preparation of Raw Materials
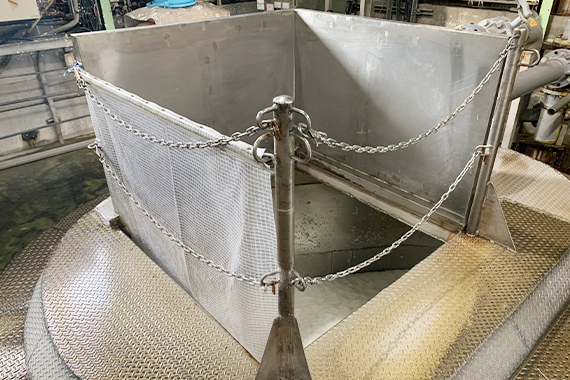
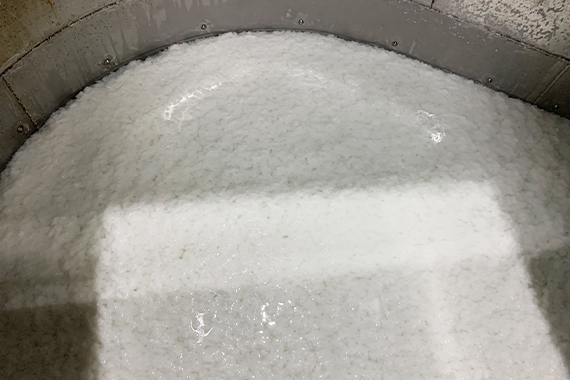
Preparation of raw materials is the process of preparing raw materials and chemicals. This is an important part because such preparation determines the basic constituents of paper. We manufacture products with various functions using our raw material preparation technologies, such as combination of different types of raw materials and blending of composite materials.
Combination of different types of raw materials
Since this technology allows to prepare the raw materials with different formulation, materials can be laminated in two layers using the combination method.
Blending of composite materials
It is possible to provide various functions to products by adding carbon fiber, graphite, activated carbon, talc, diatom earth, aramid fiber, and glass fiber.
Wire Part
The wire part is the process for the first dehydration of raw paper materials on the wire and is an important part because the materials are formed into a paper shape for the first time. We can manufacture products with various features by utilizing the cylinder, fourdrinier, inclined former, and combination.
Cylinder
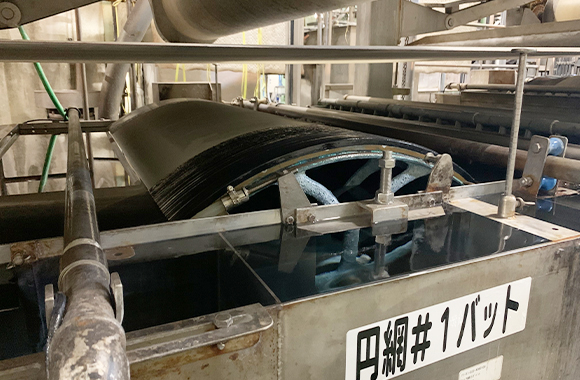
This is a former consisting of a grid-like cylinder on which a net is put up, and this forms paper layers on the surface of the cylinder using the difference in water level. Forming many layers enables to form more uniform paper layers. This cylinder manufactures papers with a wide variety of thicknesses from thin papers to thick ones like multilayer paperboard.
Fourdrinier
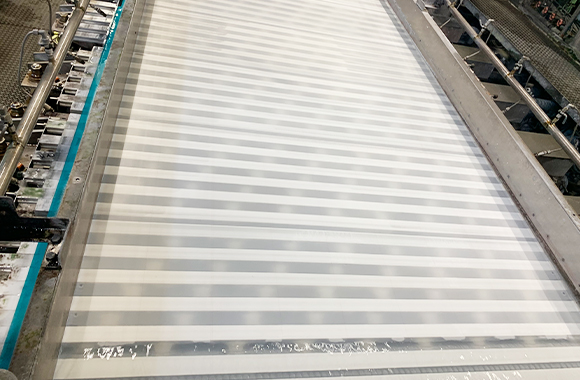
This is a former that has long endless wires that run between rolls. Raw paper materials are flown out on the wires and are then dehydrated to create paper layers. Only one material layer can create a paper with some thickness.
Inclined former
This former consists of endless long inclined wires that run. Since this former decreases the concentration of raw paper materials, it disperses long synthetic fibers evenly. This former is suitable when a texture like non-woven fabric is needed.
Combination
This technology installs multiple types of wires, such as cylinder and fourdrinier, to laminate the sheets whose paper layers were formed using the respective wires. This method combines the characteristics of the respective sheets together.
Dryer Part
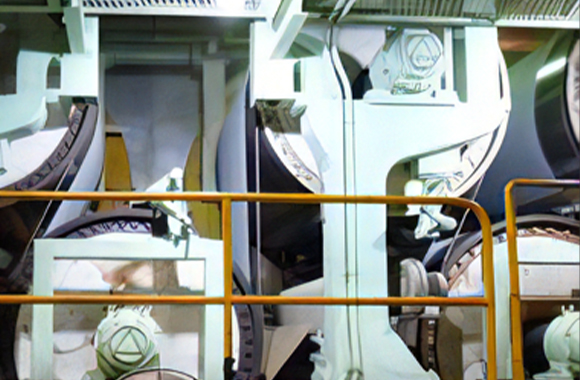
The dryer part is the process for drying the sheets that were dehydrated in the wire part. We use yankee, after, and band dryers.
Yankee dryer
This dryer has a cylinder whose diameter is as large as 2 m or larger. It dries the sheets by the heat generated by the steam supplied to the cylinder. The dryer surface is polished so that the dried paper surfaces will become glossy.
After dryer
This is a dryer with many cylinders that can dry the sheets uniformly by removing moisture a little at a time.
Band dryer
This dryer dries the sheets by blowing hot air from above and below using an endless wire mesh. This method adds a texture similar to non-woven fabric.