Processing Technology
We use a wide variety of processing technologies to add functions tailored to special application to the sheets.
Impregnation Processing
Dip-squeeze processing
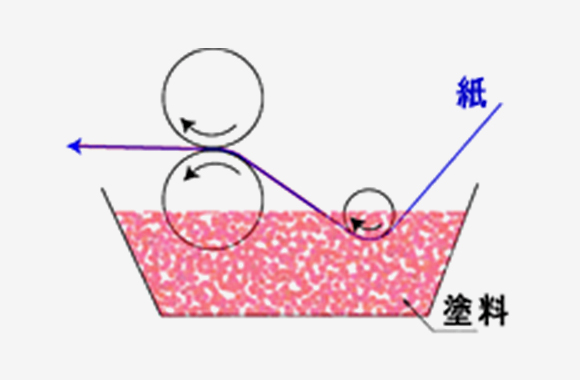
This device is for filling processing fluid of a predetermined concentration in the tray, soaking a paper or non-woven fabric with superior liquid penetration in the processing fluid, and squeezing excess liquid with the squeezing roll to attach the predefined chemical. It is characterized by the ability of processing various kinds of materials, such as water-soluble resin, emulsion resin, solvent resin, and compound resin for filler and pigment easily. In general, base materials requires the wet strength of 0.5–0.7 kgf/15 mm or higher.
Paint … It refers to the overall processing chemicals used for papermaking, such as synthetic resin solution and emulsion.
Coating
Awa Paper & Technological Company applies coatings using the comma direct, comma reverse, kiss, and gravure coating methods.
Comma reverse coating
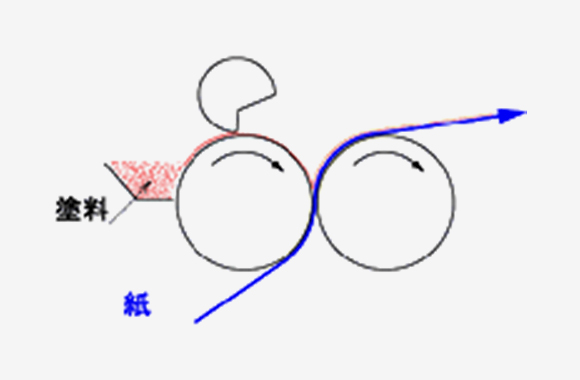
In the comma direct coating method, a processing solution is applied directly to paper. On the other hand, in the comma reverse coating method, a processing solution is once applied to rolls and then the processing solution that came out between the rod knife and roll with adjusted clearance is transferred to a paper or nonwoven fabric. This has the advantage that it is possible to apply a certain amount of processing solution accurately.
Air knife coating
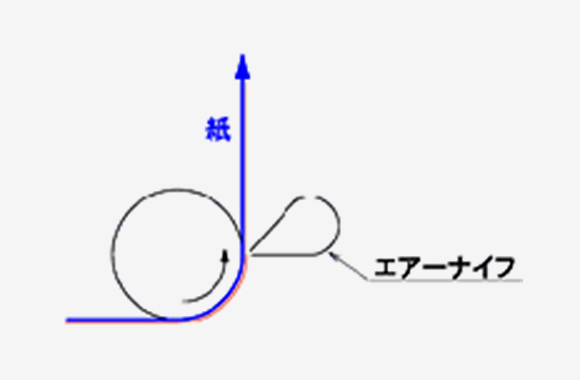
In this method, one side of a base material treated to prevent liquid from running (sizing process) in advance is kiss-coated with an excessive amount of processing solution and then the excess processing solution is scraped by pressure airflow called an air knife, which is blown onto the coated surface to adjust and make the coating amount uniform. This method is suitable for coating a base material with a rough surface with a low-viscosity solution.
Comma direct coating
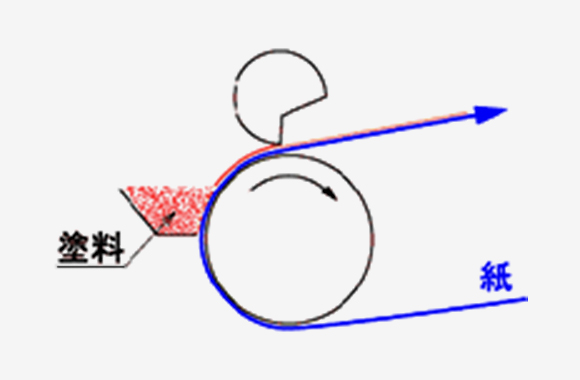
This method is a kind of knife coating, and a cutting blade similar to the one used for knife coating is incorporated into a part of the rod. This method is characterized by very high processing accuracy and the capability of processing a solution whose viscosity is as high as several thousand cps. Conversely, a processing solution with very low viscosity requires a viscosity adjustment to prevent leakage. The characteristics of the finished coating surface are that the irregularities on the base material surface are filled to make the coated surface smooth. In addition, this method is suitable for processing expensive chemicals because the processing solution in the pan can be completely used up.
Kiss coating
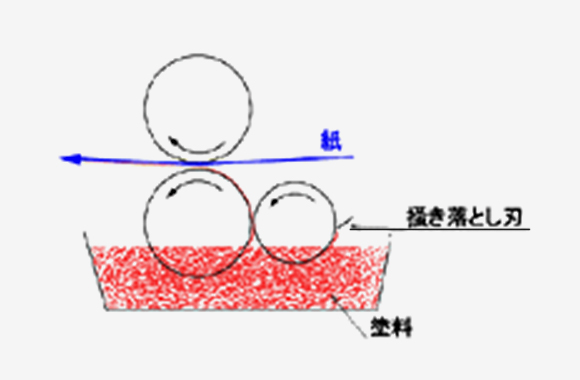
In this method, paint is lifted up by the drive rolls soaked in the paint pan, transferred to the top roll and then applied to paper that is pressed against the top roll by the press roll.
Gravure coating
This paper processing method uses the gravure roll method, which is used for printing. In this method, the processing solution is transcribed to the engraving roll and then transcribed to a base material. The advantage is that changing the pattern and depth of the engraving roll fine-tunes the coating.
Paint …It refers to the overall processing chemicals used for papermaking, such as a synthetic resin solution and emulsion.
Thermocompression Bonding and Adhesive Processing
There are two types of adhesive processing: hot-melt (processing) and hot-melt resin processing (dry method and semi-dry method).
Thermocompression bonding processing
This technology enables thermal processing utilizing the melting point of various kinds of synthetic fibers. Non-woven fabrics can be heat-set or laminated at a temperature range of 130°C to 300°C, which is equivalent to the melting point of polyethylene, polypropylene, polyester, and aramid.
Hot-melt processing
In this method, pellet-type hot-melt resin is melted in a melting apparatus and then transcribed to a base material. The resin is transcribed in either film form or fibrous form. The transcription of resin in the film form is suitable for the compounding of various functional materials and that in the fibrous form is suitable for the bonding of filter materials that require air permeability.
Hot-melt resin processing (dry method)
With this method, a hot-melt adhesive dissolved in a solvent is applied over the metal roll to vaporize the solvent for removal and then transcribed to a base material. The adhesive resin works and functions as an adhesive when reheated before use.
Hot-melt resin processing (semi-dry method)
In this method, emulsion-type adhesive resin is applied to a base material by a knife coater or roll coater to dehydrate the moisture for removal. The adhesive resin fulfills its function as an adhesive when reheated before use.
Surface Processing
Awa Paper & Technological Company performs surface processing by corrugation, embossing, and pleating methods.
Corrugation
Although corrugation generally refers to the processing of cardboard, we call the processing of cardboard flute processing to distinguish from corrugation. This processing technology is used as a method for passing a base material through two rolls with grooves engraved along the flow direction on a circle to corrugate the base material and increase the surface area of filter paper. This method is also used to prevent contact of the electrode of battery separator by changing the shape.
Embossing
In this method, designs are put on paper by passing a base material through two textured rolls. Although heat is not applied in some cases, it is generally applied in the case of deep drawing in order to retain the shape. Embossing is used either for design purposes only or for fulfilling a function.
Pleating
This processing method folds the base material like a gathered skirt in order to increase the surface area of the filter. The larger the ratio between the apparent surface area and the internal actual surface area of the filter element, the more the characteristics as a filter are shown. Therefore, this processing method is used not only for automobiles but also for air conditioning. This method requires an increase in the surface area as large as possible and a hard finish that prevents contact of the pleats.
Finish Processing
Awa Paper & Technological Company performs finish processing using winders (drum winder, center winder, and biaxial winder) and a cutter/cutting machine (guillotine).
Winder (rewinder)
This machine rewinds paper coming out of a slitter, while trimming both the width and length dimensions for completing into a product. Winders are classified into several categories according to the rewinding method.
Drum winder (surface winder)
This machine has a winder on a drum roll, and this winder is rotated and rolled up by the rotation of the drum roll. This type of machine is used widely and allows an increase in size and speed. Some have only one drum roll and others have two.
Center winder
This type of machine drives the winding shaft directly for rolling up and winds paper gently.
Biaxial winder
This machine is a kind of center winder. This machine is equipped with two winding shafts to rewind even narrow slots without overlapping by separating them into these two shafts.
Cutting machine (guillotine)
This machine cuts flat paper placed on the surface plate after the cutting process using a blade that moves up and down. It is used when the edges, corner angles, and length and width dimensions of flat paper need to be cut precisely.
Cutter
This machine cuts a continuous paper sheet into pieces of a predetermined length and width dimensions to make flat paper. In general, the cutter refers to a rotary cutter that cuts papers with a rotary blade.